Types of Product Defects
Product liability claims often revolve around the concept of product defects, which can lead to serious injuries, financial losses, and even fatalities. Understanding the types of product defects is crucial for both consumers and manufacturers to ensure safety and accountability in the marketplace. Broadly, product defects can be categorized into three main types: manufacturing defects, design defects, and marketing defects.
Manufacturing defects occur during the production process and are typically unintentional anomalies that deviate from the product's intended design. These flaws might result from substandard materials, inadequate quality control measures, or human error on the assembly line. For instance, a batch of toys may have sharp edges due to improper molding, leading to potential injuries for children. In such cases, even if only one unit in a million is defective, it can still pose significant risks and become grounds for a liability claim.
Design defects are inherent faults present in a product's blueprint before it is even manufactured. Unlike manufacturing defects that affect only specific units, design flaws impact every item produced based on that faulty design. A well-known example is the Ford Pinto case from the 1970s; the car was designed with a fuel tank placement that made it susceptible to catching fire in rear-end collisions. Despite being manufactured correctly according to its specifications, the car's flawed design posed a severe danger to consumers.
Marketing defects relate to inadequate or misleading instructions and warnings about a product's use. These deficiencies can include incorrect labeling, insufficient safety warnings, or lack of proper usage instructions that could prevent harm. Imagine an over-the-counter medication that does not adequately warn about potential side effects when taken with other common drugs; this oversight could lead to adverse reactions among users who were uninformed about the risks.
Each type of defect presents unique challenges in proving liability and obtaining compensation. Plaintiffs must demonstrate not only that they suffered harm but also establish how the defect directly caused their injury or loss. This often requires expert testimony, meticulous documentation, and sometimes navigating complex legal standards.
For manufacturers and sellers, understanding these categories underscores the importance of rigorous quality control measures and comprehensive safety testing protocols throughout all stages of production-from initial design through final distribution. It also highlights the necessity for clear communication with consumers regarding proper use and potential hazards associated with their products.
In summary, recognizing the various types of product defects-manufacturing errors, design flaws, and marketing oversights-is essential for safeguarding consumer rights and ensuring corporate responsibility within our economic system. Both parties stand to benefit from heightened awareness: consumers gain protection against harmful products while companies mitigate risk by adhering to stringent safety standards and fostering trust in their brand integrity.
Legal Theories in Product Liability Cases
Product liability cases are a cornerstone of consumer protection law, ensuring that individuals harmed by defective products can seek redress. Legal theories in product liability claims provide the framework through which plaintiffs can hold manufacturers, distributors, and retailers accountable for injuries caused by their products. Understanding these legal theories is essential for both consumers seeking justice and businesses aiming to mitigate risks.
The primary legal theories in product liability claims include negligence, strict liability, and breach of warranty. Each theory offers a different pathway to establish liability, reflecting varying degrees of fault and responsibility.
Negligence is one of the most traditional bases for product liability. Under this theory, the plaintiff must demonstrate that the defendant failed to exercise reasonable care in designing, manufacturing, or distributing the product. This could involve proving that the manufacturer did not conduct adequate testing or ignored potential safety hazards. The crux of a negligence claim lies in establishing that the defendant's lack of due care directly resulted in the plaintiff's injury.
Strict liability shifts the focus from the manufacturer's conduct to the condition of the product itself. Introduced as a more consumer-friendly approach, strict liability allows plaintiffs to recover damages without needing to prove negligence. Instead, they must show that the product was unreasonably dangerous when it left the manufacturer's control and reached them unchanged. This theory recognizes that even with best practices, some products may still pose significant risks; thus, it holds manufacturers accountable regardless of their intent or level of care.
Breach of warranty involves contractual promises regarding a product's quality or performance. There are two main types: express warranties and implied warranties. An express warranty is an explicit assurance made by the seller about certain features or functions of a product. If these assurances turn out to be false and cause harm, a breach has occurred. Implied warranties, on the other hand, arise by operation of law and include warranties of merchantability (the product will work as expected) and fitness for a particular purpose (the product will perform specific tasks). Plaintiffs claiming breach of warranty need to establish that these guarantees were unmet when they used the product as intended.
Each legal theory serves to balance interests-holding companies responsible while ensuring fairness in litigation processes. For instance, while strict liability facilitates easier recovery for injured parties by lowering burdensome proof requirements compared to negligence claims, it also imposes rigorous standards on manufacturers which ultimately incentivize safer designs and practices.
In conclusion, legal theories in product liability cases form an intricate web aimed at protecting consumers from harmful products while fostering innovation within safe boundaries for producers. By navigating through negligence claims emphasizing conduct faults or leveraging strict liability focusing on inherent dangers irrespective of fault or breaches reflecting broken promises concerning quality-plaintiffs have versatile avenues toward justice against defective goods causing them harm.
Key Elements Required to Prove a Claim
Product liability claims are an essential aspect of consumer protection, ensuring that manufacturers, distributors, and retailers are held accountable for the safety and efficacy of their products. When a product causes harm, the injured party may seek compensation through a product liability claim. However, successfully proving such a claim requires meeting specific legal criteria. This essay will outline the key elements required to prove a product liability claim.
First and foremost, the plaintiff must demonstrate that they suffered an injury or incurred damages. This injury could be physical harm, emotional distress, or financial loss resulting from using the defective product. Without proof of actual harm, there is no basis for a product liability claim. Medical records, photographs of injuries, and receipts for medical expenses can serve as evidence to substantiate this element.
The second critical element is establishing that the product in question was defective. There are three primary types of defects recognized in product liability cases: manufacturing defects, design defects, and failure to warn (also known as marketing defects). A manufacturing defect occurs when a mistake in the production process makes a particular item dangerous compared to other items made according to specifications. Design defects exist when there is an inherent flaw in the design that makes all products of that type unreasonably dangerous. Failure to warn involves inadequate instructions or warnings about potential risks associated with using the product.
To illustrate these concepts further: if a car's brakes fail due to improper installation during assembly (a manufacturing defect), it poses serious risks even though other cars of the same model function correctly. Alternatively, if all cars of a certain model have brakes prone to failure under normal conditions (a design defect), this affects every unit produced regardless of how well it was assembled. Finally, if consumers are not adequately informed about maintaining brake fluid levels leading to brake failures (failure to warn), this too can form the basis for liability.
Once it is established that there was indeed a defect present in the product at issue, causation must be proven-the defective nature of the product must have directly caused the injury or damage experienced by the plaintiff. This causation link can sometimes be complex and may require expert testimony to demonstrate how exactly the defect led to harm.
Another crucial element involves showing that at some point during its lifecycle-from manufacture through distribution-the defendant had control over or responsibility for creating or perpetuating this defectiveness within their role in bringing said item into public use domain-and thus they should bear consequent accountability accordingly based on jurisdictional rules defining scope & extent thereof vis-a-vis statutory/regulatory frameworks governing commercial practices therein relative thereto appropriately so enforced thereby effectively ensuring justice delivery mechanisms operate efficiently equitably justifiably fair manner comprehensively addressing concerns raised suitably fitting circumstances merit consideration warranted legitimately henceforth duly accorded necessary attention resolved satisfactorily concluding proceedings conclusively ultimately favoring deserving parties involved wherein applicable contingent factors prevailing adjudicated judiciously discerningly appropriately rightly altogether summarizing outcomes meritoriously befitting expectations reasonably anticipated complying standards set forth guiding principles derived underlying doctrines informing jurisprudence evolved progressively reflective social changes adapting evolving norms continually improving landscape ensuring robust safeguards entrenched protecting citizenry interests paramount importance prioritizing welfare commonweal significantly advancing societal progress holistically integrative fashion fostering sustainable development inclusive growth harmonious coexistence mutually beneficial broadly encompassing vision realized practically implementable viable solutions effectually translating ideals aspirations concrete actions impactful meaningful contributing positively enhancing quality life universally shared equitable manner abundantly enriching humanity collectively overall beneficially enduring legacy left successive generations inherit cherish preserve perpetuate responsibly prudently wisely stewarding precious resources entrusted custodianship conscientiously diligently wholeheartedly
Common Defenses Against Product Liability Claims
Product liability claims constitute a significant area of law that holds manufacturers, distributors, retailers, and others in the supply chain accountable for products that cause harm. When faced with such claims, defendants typically employ several common defenses to mitigate or eliminate liability. Understanding these defenses can provide insight into how companies navigate the complex landscape of product liability.
One of the most prevalent defenses is the "statute of limitations." This legal principle sets a specific time frame within which a plaintiff must file their claim. If this period has expired, the defendant can argue that the claim is time-barred, regardless of its merits. The rationale behind this defense is to ensure timely litigation while evidence is still fresh and available.
Another frequently invoked defense is "product misuse." Defendants may argue that the injury resulted from improper or unforeseeable use of the product rather than any defect inherent in it. For instance, if a consumer uses a lawnmower to trim hedges and gets injured, the manufacturer might argue that such use was never intended or anticipated.
"Assumption of risk" also serves as a potent defense mechanism. Here, defendants contend that plaintiffs knowingly engaged in an activity fraught with obvious dangers associated with using the product. For example, if someone participates in extreme sports using specialized equipment and sustains injuries, they may have assumed those risks voluntarily.
The "state-of-the-art" defense can be particularly compelling in cases involving cutting-edge technology or pharmaceuticals. Defendants may assert that their product was designed and manufactured according to the highest scientific and technical knowledge available at the time. This defense implies that even though safer alternatives might exist today, they were not feasible when the product was created.
Comparative negligence is another important strategy where defendants argue that the plaintiff's own negligence contributed significantly to their injury. In jurisdictions recognizing comparative fault rules, damages awarded to plaintiffs can be reduced proportionately based on their share of responsibility for the incident.
Lastly, compliance with regulatory standards often forms a robust shield against liability claims. If a company demonstrates adherence to relevant industry regulations and safety guidelines during production and distribution processes, it strengthens their position against allegations of neglect or faultiness.
In conclusion, companies facing product liability claims have an arsenal of defenses at their disposal to counter allegations effectively. From invoking statutes of limitation and arguing product misuse to leveraging state-of-the-art justifications and comparative negligence principles-each defense aims to contextualize or negate liability based on specific legal frameworks. By understanding these common defenses, stakeholders can better appreciate how businesses strive for balanced accountability while navigating potential pitfalls inherent in producing goods for public consumption.
Steps to Take if Injured by a Defective Product
When you purchase a product, whether it's a household appliance, a vehicle, or even a child's toy, the last thing on your mind is the possibility of that product causing you harm. Unfortunately, defective products do exist and can lead to serious injuries. If you find yourself in such an unfortunate situation, it's crucial to know the steps to take to protect your health and legal rights. Here are some essential actions to consider if you're injured by a defective product.
First and foremost, prioritize your health and safety. Seek immediate medical attention if necessary. Not only does this ensure that you receive the proper care for your injuries, but it also creates a documented medical record that may be vital for any future claims. Be sure to inform the healthcare provider about how the injury occurred so that they can make accurate notes.
Once you've addressed any urgent medical needs, preserve the defective product if it's safe to do so. This item will be key evidence in any legal action you might pursue. Do not attempt to fix or alter it in any way; doing so could undermine your case by making it more difficult to demonstrate how the defect caused your injury.
Next, gather as much evidence as possible related to both the incident and the product itself. Take photographs of your injuries, the defective product from various angles, and the scene where the injury occurred. If there were any witnesses present at the time of your injury, collect their contact information and ask them if they would be willing to provide statements later on.
Document everything meticulously. Keep all receipts related to your purchase of the defective product as well as any correspondence with the manufacturer or retailer about its condition or performance. Additionally, maintain a journal detailing how your injuries have impacted your daily life-this could include pain levels, emotional distress, missed workdays, and any other relevant factors.
After gathering initial evidence and documentation, consult with an experienced attorney who specializes in product liability claims. A knowledgeable lawyer can help evaluate whether you have a viable case and guide you through each step of what can often be a complex legal process. Product liability laws vary from state to state; therefore, having expert advice tailored specifically to your jurisdiction is invaluable.
Your attorney will likely advise you not to communicate directly with representatives from insurance companies or with anyone from the company responsible for manufacturing or selling the product without legal counsel present. These entities often aim to minimize their liability and might use anything you say against you later on.
As part of building your case, expect that expert testimony may be necessary-particularly from professionals who can attest to how and why the product was defective as well as explain its hazardous nature in understandable terms for judges or juries.
Finally, keep track of all expenses incurred due to your injury-medical bills, rehabilitation costs, lost wages-and compile these records carefully for potential compensation purposes.
In conclusion, being injured by a defective product is undoubtedly distressing but knowing which steps to take can significantly bolster both your recovery process and potential legal claims. Prioritize immediate medical care first before preserving evidence meticulously; consult with specialized legal counsel promptly; avoid direct communication with potentially liable parties without representation; prepare for comprehensive documentation requirements-and throughout this journey-remain vigilant about protecting both your physical well-being and legal rights.
Potential Compensation and Damages
Product liability claims are a significant area of law that can have profound financial and legal consequences for businesses and manufacturers. When consumers are harmed by defective or unsafe products, they have the right to seek redress through the legal system. Two of the primary forms of redress in these situations are potential compensation and damages.
Potential compensation refers to the monetary recovery that a plaintiff may receive as a result of a product liability claim. This compensation is intended to cover various kinds of losses suffered due to the defective product. These losses can be both economic and non-economic in nature. Economic losses typically include medical expenses, lost wages, and costs associated with repairing or replacing damaged property. Non-economic losses might encompass pain and suffering, emotional distress, loss of consortium, and other types of personal harm that do not have a direct monetary value but significantly impact the victim's quality of life.
In addition to compensatory damages, plaintiffs in product liability cases may also seek punitive damages. Unlike compensatory damages which aim to make the injured party whole again, punitive damages are designed to punish the wrongdoer for particularly egregious conduct and deter similar future behavior. Courts award punitive damages in cases where it is demonstrated that the defendant acted with gross negligence, malice, or reckless indifference to consumer safety.
The process for determining potential compensation involves several steps. Initially, an assessment is made regarding whether the product was indeed defective and whether this defect directly caused harm to the consumer. Legal standards such as strict liability often apply in these cases; under strict liability, a manufacturer can be held liable for defects regardless of fault or intent.
Once liability is established, quantifying damages becomes crucial. Plaintiffs must provide evidence supporting their claims for economic losses through medical records, employment documentation, receipts for out-of-pocket expenses, and expert testimony if necessary. Non-economic damages require a more subjective analysis but can be supported through personal testimonies about how the injury has impacted daily life.
It is also important to consider that different jurisdictions may have varying laws governing product liability claims which could influence both eligibility for compensation and the amount awarded. Some states impose caps on certain types of damages while others might follow comparative negligence rules affecting how much a plaintiff can recover if they are partially at fault.
Moreover, settlements outside court are common in product liability cases as companies often prefer to avoid lengthy litigation processes which can be costly and damaging to their reputation. Settlement negotiations involve both parties agreeing on a fair amount based on projected trial outcomes without admitting fault publicly.
In conclusion, potential compensation and damages in product liability claims serve critical roles in providing justice for injured consumers while holding manufacturers accountable for ensuring product safety. They encompass both tangible financial recompense for actual losses incurred as well as broader considerations like punitive measures meant to enforce higher standards within industries producing consumer goods. As such claims continue evolving with new products entering markets rapidly increasing technological advancements scrutiny over ensuring consumer protection remains paramount.
Notable Case Studies and Precedents
Product liability claims have long been a cornerstone of consumer protection law, ensuring that manufacturers are held accountable for the safety and efficacy of their products. Over the years, several notable case studies and precedents have shaped the landscape of product liability, influencing both legal standards and corporate practices.
One of the most seminal cases in product liability history is Greenman v. Yuba Power Products (1963). In this landmark decision, the California Supreme Court established the doctrine of strict liability for defective products. The plaintiff, William Greenman, was injured while using a power tool manufactured by Yuba Power Products. Despite following all instructions and precautions, a defect in the tool caused severe injuries. The court ruled in favor of Greenman, asserting that manufacturers must be responsible for any defects that cause harm, regardless of whether they exercised care during production. This case set a powerful precedent by prioritizing consumer safety over manufacturer negligence.
Another pivotal case is Liebeck v. McDonald's Restaurants (1994), often referred to as the "hot coffee case." Stella Liebeck suffered third-degree burns when she accidentally spilled scalding hot coffee purchased from a McDonald's drive-thru onto her lap. The jury awarded her $2.86 million in compensatory and punitive damages after discovering that McDonald's coffee was served at temperatures far higher than industry standards, posing an unreasonable risk to consumers. This case not only highlighted issues regarding corporate accountability but also sparked debate on tort reform and frivolous lawsuits.
In more recent times, the litigation surrounding Johnson & Johnson's talcum powder has garnered widespread attention. Numerous plaintiffs claimed that prolonged use of Johnson & Johnson's baby powder led to ovarian cancer due to asbestos contamination-a known carcinogen. In 2018, a Missouri jury awarded $4.7 billion in damages to 22 women who developed ovarian cancer after using the product for decades. Although Johnson & Johnson continues to deny any wrongdoing and has appealed multiple verdicts, these cases underscore significant concerns about transparency and public health.
The Vioxx scandal involving Merck & Co., Inc., further illustrates how pharmaceutical companies can face extensive legal repercussions over product safety issues. Vioxx was a widely prescribed painkiller withdrawn from the market in 2004 after studies revealed it significantly increased risks of heart attacks and strokes among users. Merck faced thousands of lawsuits alleging they knew about these dangers but failed to adequately warn consumers or healthcare providers. The company eventually agreed to a $4.85 billion settlement in 2007-one of the largest pharmaceutical settlements ever-which served as a stark reminder about ethical responsibilities within drug manufacturing.
These case studies collectively highlight crucial aspects of product liability claims: strict liability principles established through Greenman v. Yuba Power Products; corporate accountability emphasized by Liebeck v. McDonald's Restaurants; public health concerns illustrated by Johnson & Johnson's talcum powder litigation; and ethical obligations underscored by Merck's handling of Vioxx-related risks.
As society continues evolving with advancements in technology and medicine, so too will challenges related to product safety emerge anew-making it imperative for legal frameworks surrounding product liability claims remain robust yet adaptable enough address emerging threats effectively while safeguarding consumer interests at all times.
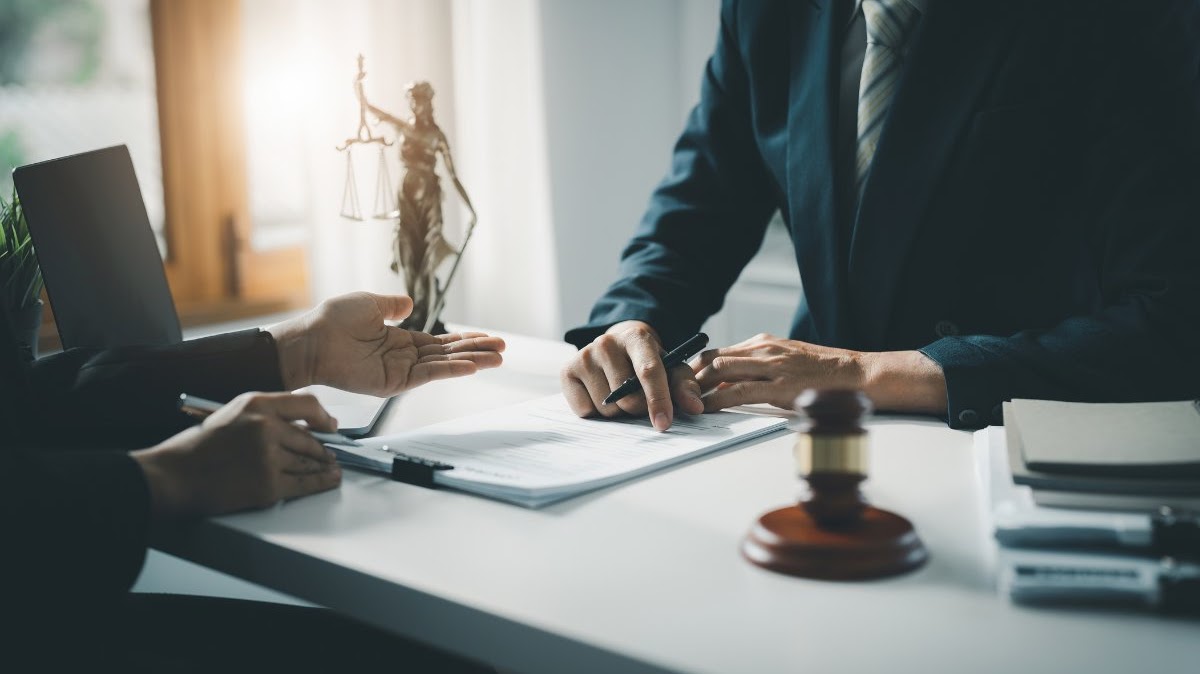